
JOHN W. EVERT | Mechanical Engineering Technology
Testing
Phase 1 - Dimensionality
-
Must measure 11.75” diameter x 1.25” wide
-
Rotor body must mount to a hub carrier with eight 5/16” fasteners on a 7-inch bolt circle.

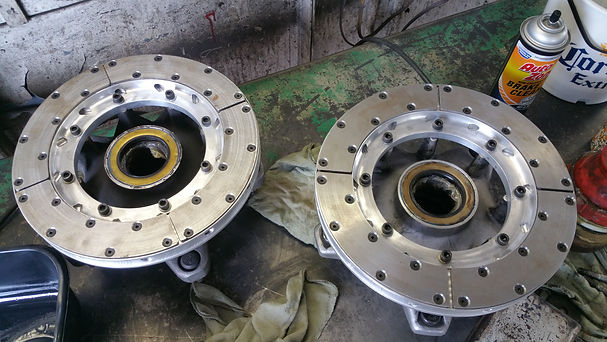

Phase 2 - Off-car testing
-
Reduce the static mass by 20%.
-
Was only able to acheive a 12% reduction in mass (12.9lbs vs 11.35lbs)
-
-
Confirm an existing manufacturer’s claim of 34% reduction in the moment of inertia. Litebrake.com
-
Material selection and careful machining was only able to reduce Moment of Inertia by 24%
-

Phase 3 - On-car testing
-
Rotor assembly must be able to resist the forces created by an angular velocity of 315 rad/sec (3000RPM)
-
AT 100MPH, rotor/wheel is spinning at ~1200RPM
-
-
Dissipate the heat generated from 125 kilowatts of kinetic energy if mounted on the front axle of the racing car
-
Repeatedly. For 74 laps until the rotor body warped.
-
-
Rotor must be able to resist the torque provided by the linear deceleration rate of 8 m/s^2
-
GPS Telemetry shows that entry/exit speeds and braking zone times are reasonaly consistent to provide proof of such a deceleration event
-
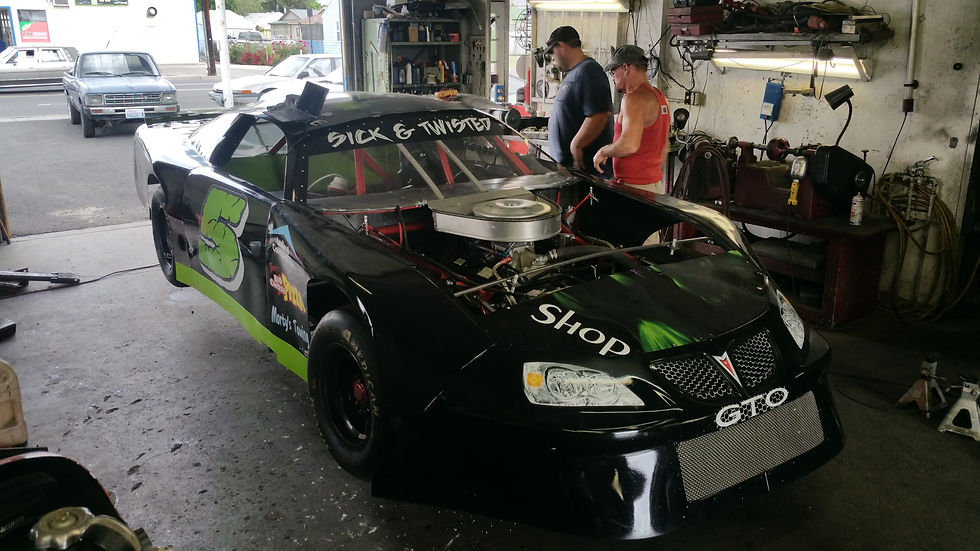

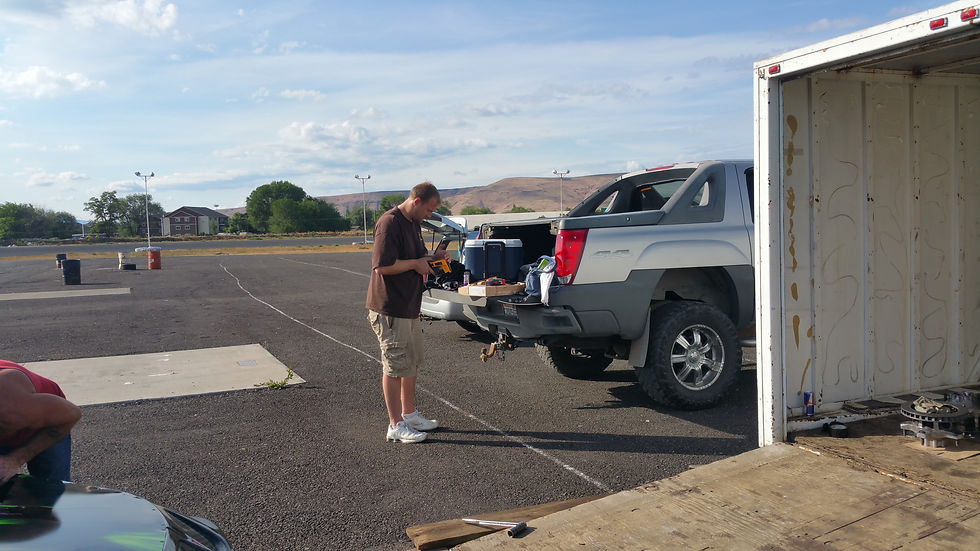
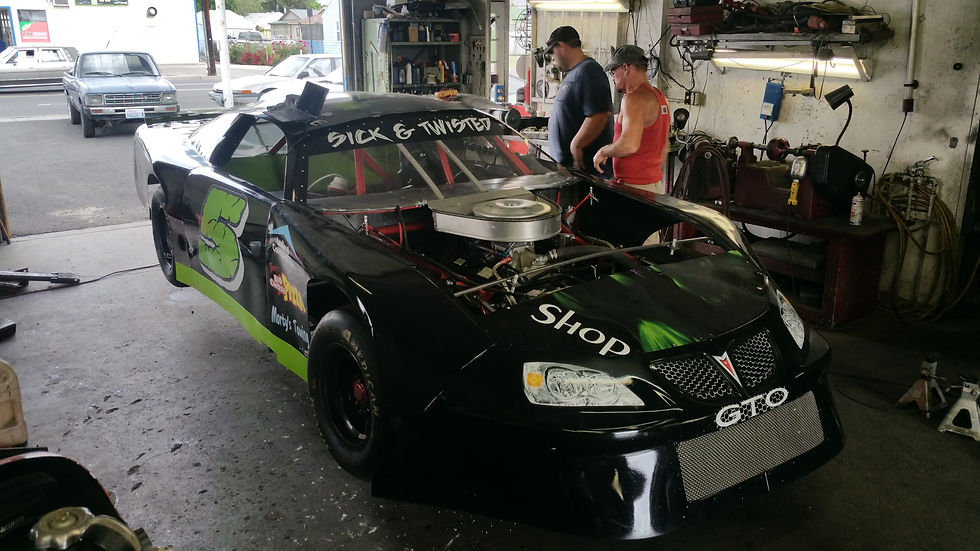